摘 要:本文介紹了渦流檢測技術原理及主要特點,提出在役換熱器換熱列管的檢測實施要點,并就該技術在合成氨裝置中的實際檢測應用作簡要介紹。
關鍵詞:換熱列管 渦流檢測
0 前 言
在合成氨生產裝置中,廣泛使用著各種形式的列管式熱交換器,其中有不少換熱器在高溫、高壓及腐蝕介質中運行。由于介質腐蝕、沖刷、疲勞應力等作用,會使列管管壁產生各種腐蝕缺陷、損傷和壁厚減薄,這將嚴重威脅設備的安全運行。
而由于設備結構的特殊性或系統裝置條件的不具備,很多換熱器不能進行常規的殼側水壓或氣壓試驗,無法準確查找出換熱管的泄漏部位,更不能對換熱列管可能存在的隱患作出有效的預報性診斷。
因此,采用渦流檢測技術對這些在役換熱器的換熱列管進行定期檢測,掌握列管缺陷的存在及發展情況,掌握列管最小壁厚值的變化情況,從而對換熱列管使用狀況作出有效的預防性診斷及處理,是保證裝置生產設備長周期安全運行的可靠技術手段。
1 渦流檢測技術原理
渦流檢測技術的理論基礎是電磁感應。
載有交變電流的檢測線圈靠近導電試件時,由于激勵線圈磁場的作用,將會在試件中感應出渦流(見圖1);而渦流的大小、相位及流動形式受到試件導電性能的影響,同時產生的渦流也會形成一個磁場,這個磁場反過來又會使檢測線圈的阻抗發生變化。
通過測定檢測線圈阻抗的變化,就可以判斷出被測試件的性能及有無缺陷。
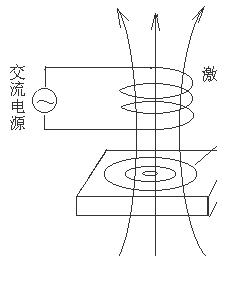
圖1 渦流檢測的原理
對在役換熱列管的渦流檢測,采用內穿過式線圈作為“檢測探頭”,通常由兩個或兩個以上的測量線圈組成。
對列管進行渦流檢測時,線圈中加載的交變電流將在列管壁上形成渦流場(見圖2);而列管的幾何缺陷、電磁異常和壁厚變化等因素都將對該渦流場形成影響。
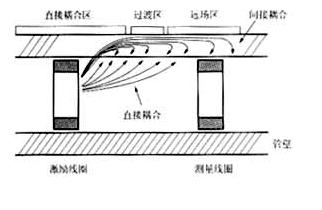
圖2 列管渦流場形成示意圖
當列管無影響渦流場的因素存在時,渦流場無變化,兩個測量線圈反向連接感應電壓為平衡狀態,沒有輸出;當列管存在影響渦流場的因素時,渦流場的變化又使測量線圈的阻抗和感生電壓發生改變。
測出阻抗變化量,經過儀器處理可判列管的缺陷情況——渦流探傷;
測出感生電壓變化量,就可得出列管壁厚的變化狀況——渦流測厚。
2 渦流檢測技術類型
渦流檢測技術手段分為兩大類型:常規渦流檢測和遠場渦流檢測。
2.1 常規渦流檢測
適用于純奧氏體不銹鋼、純鈦及其合金、純鎳及其合金、銅、鋁等非鐵磁性材料。
常規渦流場形成于“近場區”,其渦流信號具有趨膚效應及在深度方向的相位滯后效應。
利用相位滯后效應,在檢測參數合適的前提下,通過建立對比試樣管上不同深度人工模擬缺陷的阻抗圖及缺陷深度—相位圖(見圖3、圖4),可在渦流探傷時有效區分列管壁缺陷的性質及類型。
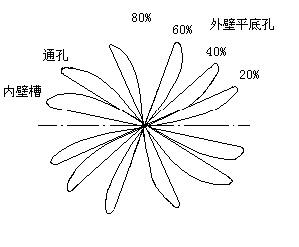
圖3 常規渦流缺陷阻抗圖
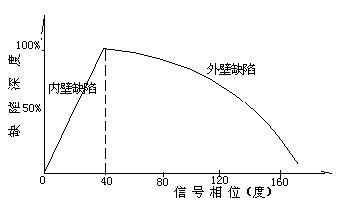
圖4 常規渦流缺陷深度—相位曲線圖
2.2 遠場渦流檢測
遠場渦流技術基于一種特殊物理現象——遠場渦流效應,是一種能穿透金屬管壁的低頻渦流檢測技術。
特別適用于奧氏體-鐵素體雙相不銹鋼、鐵素體不銹鋼、Cr-Mo鋼、碳鋼等鐵磁性材料。
檢測換熱列管時,內置式探頭置于被檢測管內,探頭上有一個激勵線圈,還有一個(或二個)測量線圈;激勵線圈和測量線圈的距離為列管內徑的2-3倍。
激勵線圈通以低頻交流電,發出的磁力線(能量)穿過管壁向外擴散,在遠場區又再次穿過有表面缺陷的管壁向內擴散,被測量線圈接收(見圖5)。
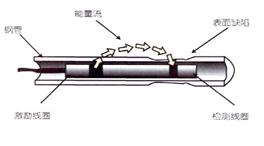
圖5 遠場渦流場能量傳遞示意
若管子壁厚為h,則磁場兩次穿過管壁造成的振幅衰減和相位滯后由下式決定
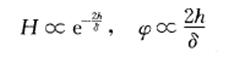
H—磁場強度振幅衰減值
δ—集膚深度
φ—測量線圈感應電壓和激勵電流間的相位滯后值
由上式可見:若管壁存在裂紋、凹坑及腐蝕等缺陷,則相應部位管壁厚度減小,導致檢測信號相位滯后值減小,振幅衰減值增大。
據此,可以根據檢測信號相位及幅值的變化,判斷被檢測換熱管缺陷狀況。
2.3 遠場渦流和常規渦流技術的比較
1)測量磁場區域:
常規渦流線圈置于直接耦合區,測量的是傳播到管壁又直接返回的磁場。
遠場渦流為避免直接磁耦合,測量線圈必須置于遠離激勵線圈的間接耦合區,測量穿過管壁后在管外沿管軸傳播一段距離返回管內的磁場。
因此,遠場渦流檢測獨具有透壁性,能檢測整個管壁上的缺陷而不受集膚效應的限制,克服了電導率和磁導率的影響,對內外壁的缺陷具有相同的靈敏度,且相位信號不受提離效應的影響。同時,對填充系數要求低,對探頭在管內行走產生的偏心影響很小。
2)檢測頻率:
遠場渦流檢測采用較低的頻率(典型為50~500Hz),磁場穿過鐵磁性材料管壁,不受管壁厚度影響。
常規渦流檢測頻率較高(千赫范圍),受趨膚效應制約,磁場被限制在管壁有限厚度內,檢測厚壁列管外部缺陷較為困難。
3 渦流檢測技術特點
3.1 渦流技術在換熱列管檢測應用中的優越性
1)非接觸式無損檢測,是檢測在役換熱列管的最行之有效手段。
2)檢測速度快,靈敏度高。
3)檢測信號為電信號,可進行數字化處理,便于存儲、再現及進行數據比較和處理。
4)渦流探傷時,通過對檢測信號的相位-幅值分析,可就缺陷信號所表征的缺陷性質、類型、大小進行有效判定。
5)渦流測厚時,可實時顯示換熱列管全長的壁厚分布狀況,并自動記錄最薄截面的壁厚數據為檢測值,測量誤差在±0.05mm內。
3.2 渦流技術在換熱列管檢測應用中的局限性
1)需要制作專門的對比樣管進行檢測基準的校準。
2)受渦流所特有的末端效應的影響,離換熱管口一定范圍內檢測信號將嚴重畸變,無法正確識別出缺陷,一般稱此部位為渦流檢測的“盲區”。
3)對于U型管,由于探頭自身的長度與剛性原因,無法穿入U型彎管的中心較小彎曲半徑段,故此區域管段無法進行渦流檢測。
4)渦流檢測信號只表征換熱列管母材自身的變化狀況,無法反映出管子-管板角焊縫的狀態,不能用于查找角焊縫的相關缺陷。
5)采用內穿過式線圈時,對缺陷所處圓周上的具體位置無法判定;采用旋轉探頭式檢測雖可定位,但檢測速度慢。
4 渦流檢測系統組成
渦流檢測系統由檢測主機、數據分析系統、檢測傳感器(探頭)及對比樣管組成。
4.1 檢測主機(以ET556H為例)
用阻抗平面顯示,能實時得到缺陷信號的李薩育圖形,全面反映檢測信號的幅值、相位。
利用相位分析技術,可將干擾與缺陷信號分開,提高信噪比。
激勵頻率范圍寬廣可調(50Hz~1MHz),相位3600可調范圍。
采用自動平衡技術。
具備多頻檢測功能,可以有效抑制干擾
4.2 數據分析系統
利用計算機進行檢測信號處理,具備混頻、報警設定、相位-幅值分析、數值存儲記錄等適時數據自動分析處理功能。
采用專門開發設計的檢測軟件,可自動完成換熱列管壁厚的求平均值、分類、統計等工作,并生成各類直觀的數據分布圖;通過對分布圖的分析,可以了解設備管子的壁厚分布情況和腐蝕情況,從而分析引起腐蝕的設備和工藝因素。
4.3 檢測傳感器
渦流探傷時,采用自比較式差動線圈;渦流測厚時,采用絕對式線圈。
一般情況下采用普通內穿過式,特殊情況下采用內壁旋轉探頭式。
4.4 對比樣管
用來校驗儀器檢測參數,保證檢測模型的精確性。
通常采用與被檢測換熱器列管相同材料及規格的管段進行加工,特殊情況下可代用,但必須由具有豐富檢測經驗的技術人員依據理論計算值進行檢測偏差調整。
對比樣管按相關標準規定結構形式,根據具體檢測要求進行設計;采用數控、線切割等高精尖加工手段,控制加工誤差滿足相關標準的規定。
檢測使用的對比樣管,必須能準確模擬被檢換熱列管的各種可能缺陷、壁厚減薄范圍。
5 在役換熱器列管渦流檢測的目的及內容
5.1 檢測目的
對在役換熱器的換熱列管進行渦流檢測,實現一下檢測目的:
1)可估價換熱列管的全面工作狀態,并通過常規檢查來評價某種狀態可能進一步惡化的情況。
2)定量評價由于水或溶液的化學成分和設備運行情況的變化而使換熱列管產生變化的狀態、變化的速率以及設備的腐蝕速率,推算換熱器列管的剩余壽命。
3)研究整個換熱器換熱列管的缺陷和腐蝕的分布狀態,以幫助分析并確定引起換熱器的狀態惡化及泄漏的原因。
4)為確定是否需要修理和進一步在適當的時候換管提供有用的資料。
5.2 檢測內容
1)渦流探傷:檢測換熱列管是否存在裂紋、蝕坑、機械損傷等缺陷,評定缺陷的類型、大小及性質。
2)渦流測厚:檢測換熱列管全長的壁厚變化狀態,準確查找出最薄截面位置并確定殘余壁厚值,判斷列管壁的腐蝕狀態、腐蝕程度。
3)綜合以上兩項檢測內容,可準確判斷本次檢測時是否存在需要報廢處置的部件或設備,并預判在下一運行周期內換熱列管可能的腐蝕發展或是否可能出現泄漏,為換熱器安全運行提供可靠依據。
6 在役換熱器列管渦流檢測的實施要點
6.1 檢測方案的制訂
不同工藝介質及運行特點、不同換熱列管材質及壁厚的換熱器,其主要腐蝕特征及損壞形式均不相同。
因此,必須根據設備結構特點及工藝運行狀況、換熱列管材質及壁厚、換熱列管表面狀態等因素,結合相應的檢驗標準或規范,綜合制訂檢測方案。
在檢測方案中,需規定:檢測主要目的、檢測系統、檢測參數、檢測程序、檢測評判標準及檢測報告形式。
6.2 對比樣管的標定
對比樣管的標定信號為現場檢測信號分析處理的基本依據。
檢測前,必須先通過檢測頻率、相位、增益等參數的設定,將對樣管進行標定,獲得最佳檢測信號,以建立有效的檢測數據模型。
6.3干擾的抑制
由于換熱列管周圍有管板和支撐板環繞,將會對檢測造成一定干擾。如果列管上恰在此部位存在缺陷,則干擾信號將會與缺陷信號疊加形成復合信號而難于判別,有時甚至會淹沒缺陷信號,因此必須抑制干擾。
常用的有效方法是采用混頻技術。
6.4 渦流探傷缺陷的評定
對檢測發現的缺陷信號進行評定是渦流探傷最關鍵的技術,尤其對多信號疊加形成的復合信號更難于分辨。
這就要求技術人員有豐富的檢測經驗和對所測設備的充分了解,
在實際檢測中,常規渦流由于存在集膚效應及深度方向的相位滯后,因此用對比試樣對檢測系統進行合適的調試后,依據缺陷信號的相位及幅度大小,可明確地區分缺陷的位置及深度,即缺陷是否穿透,是位于管子的內壁還是外壁及其大小等。
遠場渦流檢測技術由于不存在常規渦流檢測的集膚效應及深度方向的明顯相位滯后,因此通過相位變化來區別缺陷位于換熱管的內壁或外壁較為困難,也不能準確確定缺陷深度;只能通過實際檢測信號與模擬缺陷信號在相位和幅值上的差異,分析缺陷造成的金屬損失體積量,從而 “當量”評判缺陷程度。
由于遠場渦流場分布的特點,即使換熱管上體積損傷量相同的缺陷,由于在分布方向和表現類型上的不同,也會影響缺陷的檢出和判定。
若換熱管上缺陷相當接近其鐵磁性材料制作的支撐板,則受場效應的影響,支撐板信號將嚴重干擾實際缺陷信號,造成實際缺陷的有效檢出及正確識別相當困難。與此類似,管束邊緣的換熱管,其缺陷信號也容易受到設備筒體上鐵磁性結構件的信號干擾。
遠場渦流檢測時,對換熱管軸向裂紋的漏檢可能性比較大。這是由于激勵線圈產生的電磁場沿換熱管軸向平行傳播,對于換熱管軸向裂紋,一方面其總的金屬體積損失量較小,另一方面缺陷切割場流較小,在探頭上激勵的相對電壓變化較低,測量線圈接收信號不大明顯。
6.5 渦流測厚數據分析
渦流測厚時,事先在軟件內輸入換熱器管板圖文件,按一定次序逐根檢測,數據分析系統直接讀取渦流信號并顯示為測厚曲線,同時轉換成壁厚數值并實時對應顯示、存儲。
渦流測厚軟件所記錄的壁厚數值,為此列管的最薄截面的壁厚平均值;同時,在檢測過程中依據測厚曲線的變化,可分析列管全長的壁厚變化趨勢。
受現場環境因素的影響,渦流測厚曲線有時會發生漂移,從而導致檢測誤差的存在。這就要求檢測人員能迅速判斷出此誤差并及時采取措施糾正測厚曲線的漂移,以保證檢測模型的穩定性
7渦流檢測技術在合成氨裝置在役換熱列管中的工程應用實例
7.1檢測工程業績簡介
作為國內最早在石化行業進行在役換熱列管渦流檢測工程應用的檢測單位之一,重慶奧林特機電技術有限公司運用常規和遠場渦流檢測技術,在全國范圍的不同領域進行了大量的渦流檢測工程實踐;尤其是在具有較大技術難度的鐵磁性材料換熱列管遠場渦流檢測方面,積累了豐富的經驗。
公司在換熱列管渦流檢測方面所服務的領域包括石油、石油化工、化肥、甲醇及其他各不同類型化工裝置,服務廠家包括國外獨資、中外合資、大型國企等中外知名企業,并與中石油、中石化、巴斯夫、BP等世界性大公司形成了長期合作伙伴關系。
檢測換熱器近200臺次/年,檢測的換熱列管材料包括純奧氏體不銹鋼、銅合金、純鈦及鈦合金、純鎳及鎳基合金、哈氏合金、鋯-不銹鋼復合金屬等非鐵磁性材料和碳鋼、鉻鉬鋼、鐵素體-奧氏體雙相不銹鋼等鐵磁性材料,涉及的換熱管形式有直管、U型管、翅片管,換熱器型式有固定管板式、浮頭式、U型管式。
在合成氨生產裝置中,我們已經成功地對以下在役換熱器列管進行了多次渦流檢測:
第一廢熱鍋爐、第二廢熱鍋爐、合成再沸器、冷卻水處理器、碳酸鉀溶液再沸器、碳酸鉀溶液輔助再沸器、分子篩再生加熱器、再生塔再沸器、原料氣及循環氣一段氨冷器、原料氣及循環氣二段氨冷器、原料氣及循環氣三段氨冷器、氨合成塔進氣原料氣換熱器、氨合成塔進氣出氣換熱器、氨合成塔出口鍋爐給水換熱器、惰性氣洗滌器、冷水加熱器、合成氣水冷器、氨壓機出口氨冷器、氨合成塔底部換熱器、水煤氣換熱器、低壓廢熱鍋爐等。
7.2檢測應用實例
1)常規渦流探傷:
以某廠合成再沸器(105CB)檢測為實例。
該換熱器為浮頭式,換熱列管材料為SA249 TP316SS型不銹鋼,規格¢19.05×1.65×4000,共2400根,其中檢測前已堵管22根。
換熱器管程介質為MDE溶液,殼程介質為變換氣(氮氣、氫氣)。
檢測時,采用ET-556型數字多頻渦流儀,對比樣管為TP316L型不銹鋼,規格¢19.05×2.11 孔型,檢測傳感器為高頻差動內穿過式,人工拉動探頭。
經參數調節后,獲得對比試樣管上人工模擬缺陷檢測信號阻抗圖類圖3,并據此建立缺陷信號深度-相位曲線圖類圖4。
實際檢測結果為:12根列管存在可計性缺陷信號,其中A級缺陷8根,D級缺陷4根。
其中:管號為55-26的列管,于離下管口約1.5米附近,獲得缺陷信號阻抗圖如圖6。
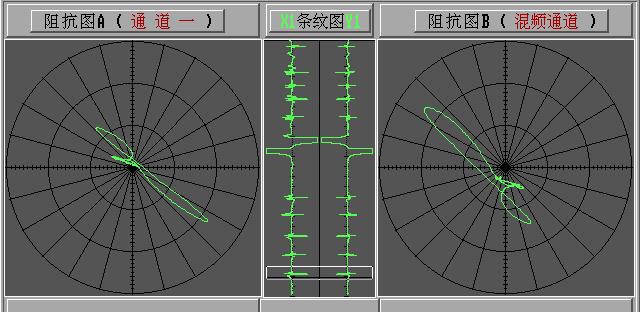
圖6 合成再沸器列管55-26渦流探傷信號
檢測判定該缺陷級別為D級,具備穿透性;抽出列管后證實檢測判定無誤(見圖7)。
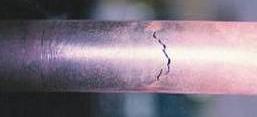
圖7 合成再沸器列管55-26穿透性裂紋
2)遠場渦流探傷:
以某廠合成氣廢熱鍋爐檢測為實例。
該換熱器為固定管板式,列管材料為16Mo3,規格¢30×2.5×5400,共876根。
管程介質為工藝合成氣,殼程介質為蒸汽。
檢測時,采用ET-556型數字多頻遠場渦流儀,對比樣管為16Mo3 ¢30×2.5 模擬缺陷分布為通孔、平底孔、環槽、平槽,檢測傳感器為內穿過式,人工拉動探頭。
經參數調節后,獲得對比試樣管上人工模擬缺陷檢測信號阻抗圖如圖8~11。
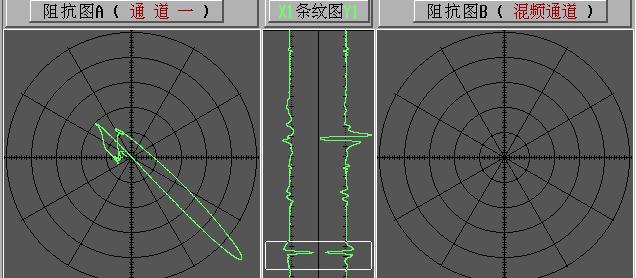
圖8 對比試樣上通孔信號
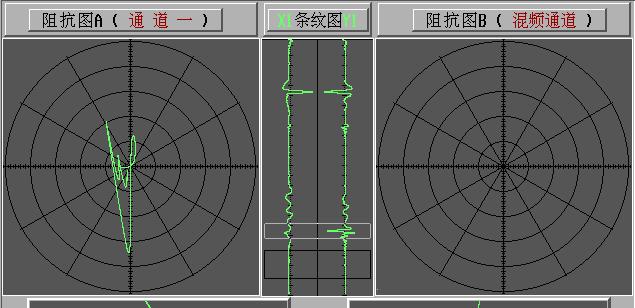
圖9 對比試樣上40%單邊銼槽信號
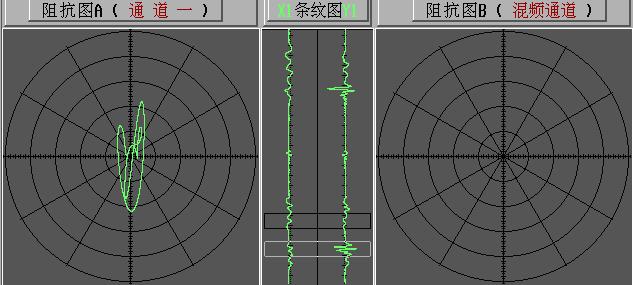
圖10 對比試樣上20%平底孔信號
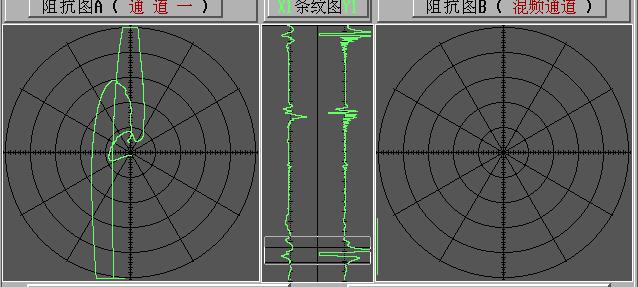
圖11 對比試樣上20%環槽信號
實際檢測結果為:25根列管存在可計性缺陷信號。
其中:管號為25-12的列管,于離下管口約1.2米處,獲得缺陷信號阻抗圖如圖12。
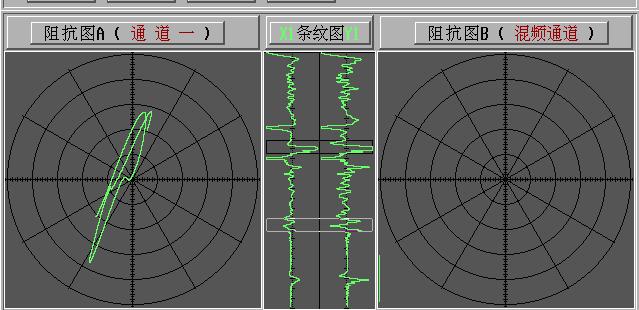
圖12 合成氣廢熱鍋爐列管25-12渦流探傷信號
可以看出:缺陷信號幅值接近于對比樣管上20%平底孔人工缺陷,但相位角大于20%環槽人工缺陷。
檢測判定該缺陷深度不到壁厚的20%,系外壁磨蝕造成的局部淺表缺陷。
3)渦流測厚:
仍以某廠合成氣廢熱鍋爐檢測為實例。
檢測時,采用ET-556型數字多頻遠場渦流儀,對比樣管為16Mo3 ¢30×2.5 厚度為2.5/2.0/1.5,檢測傳感器為內穿過式,人工拉動探頭。
檢測結果統計為:最大壁厚2.60 mm,最小壁厚2.05 mm,平均壁厚2.44 mm。
檢測獲得某列管測厚曲線如圖13。
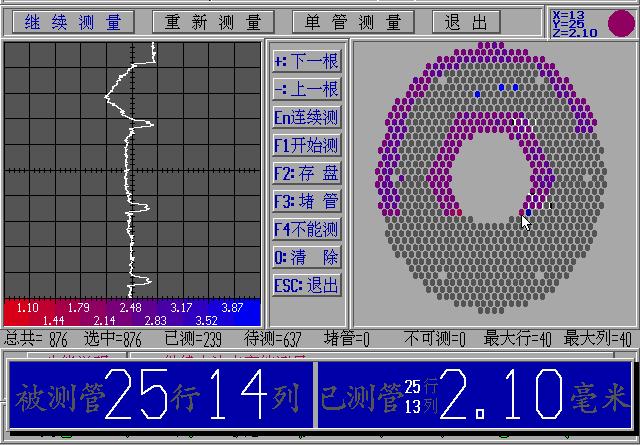
13 換熱列管渦流測厚曲線
儀器自動記錄最薄截面平均值2.10mm為該列管壁厚測量值。
由圖13可以分析出:該列管存在明顯減薄區,減薄區位置在下管口往上600~1000mm范圍;與同一列管上其他壁厚均勻的管段部分相比,減薄值在0.3mm~0.35mm左右。
全部被檢列管的壁厚數據分布圖見圖14。
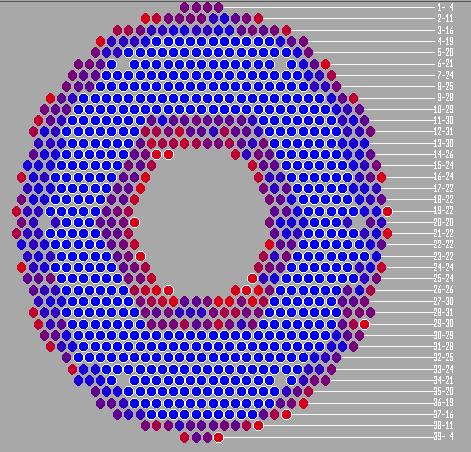
圖14 換熱列管渦流測厚數據分布管板圖
結束語
1)作為一種先進的無損檢測技術手段,渦流檢測技術對在役換熱器換熱列管的檢測具有不可替代的應用前景。
2)多年的檢測經驗表明:有計劃地對重要設備進行定期檢測,能夠預先發現潛在的缺陷,掌握設備的實際腐蝕狀況并預測其殘余壽命。