1969年捷克化工與荷蘭斯塔米卡本公司簽訂了專利與技術轉讓協議,同意捷克化工采用先進的二氧化碳氣體工藝。對于尿素裝置,捷克化工的工程設計和開車服務一直非常成功。
1970年捷克化工與東德的工業肥料制造商VEB STICKSTOFWERK PIESTERITZ公司簽訂了第一和第二個合同。兩個合同涉及三個裝置,每個裝置日產達到1050噸且成功開車。之后捷克化工設計新建了許多尿素裝置,迄今為止成功完成了19個用荷蘭斯塔米卡本公司工藝的尿素裝置。
捷克化工是荷蘭斯塔米卡本公司指定的總承包商之一。我們設計的尿素裝置的日產總值達到19920噸,占目前世界上用荷蘭斯塔米卡本公司工藝的尿素裝置的15%。捷克化工設計的裝置日產能力范圍為1000-1670噸。其中有六個裝置采用晶結化與融化造粒工藝,生產縮二脲的含量較低。其他裝置采用常規的蒸發和融化造粒工藝,生產標準含量的縮二脲尿素。
Top Urea technology 2000 plus TM
捷克化工具有設計和提供用荷蘭斯塔米卡本公司最先進的工藝Urea 2000 plus(tm)尿素裝置的資質。這種生產尿素的新工藝改善了二氧化碳氣體工藝,特別是采用了一些新的設備(如池式冷凝器,池式反應器)和一些其他的重要的改進措施。這些改進降低了氣體工藝合成部分的投資成本,同時也提高了整個裝置的可靠性。改進后的其他工藝的投資成本并不會受到影響。新工藝的原料和輔料消耗低,同時操作彈性幅度大以及運轉成本低。
荷蘭斯塔米卡本公司改善二氧化碳氣體工藝可由以下方式實現。
適合舊尿素裝置的擴能,安裝高壓池式冷凝器。
池式冷凝器特點是容積更大,操作溫度更高,壓降更低,冷卻面積更小。同時氨氣與二氧化碳的比率偏差相對于原工藝敏感性降低。
池式冷凝器是水平安裝的。管程生產低壓蒸氣(4bar),管束周圍的氣相部分冷凝,同時產生氨基甲酸酯、未合成氨和二氧化碳在池式冷凝器中充分混合。在此過程中氨基甲酸酯與水脫離,產生尿素。池式冷凝器的反應容量較大,整個反應可以達到平衡。由于池式冷凝器的水平安裝明顯的降低了整個裝置的高度。
安裝新的高壓池式反應器改變了整個合成部分的理念,用池式反應器簡單化了原先的高壓合成部分,與舊工藝相比只保留二氧化碳氣體的優勢沒有變化。二氧化碳氣體部分的排氣在冷凝池式反應器里面。通過此方式我們就實現了在同一水平的反應器中流程的兩個步驟。除了保留原池式冷凝器的優勢之外,新的池式反應器還具有低投資成本的優勢。投資降低的原因是由于不需要較貴的高壓容器、高壓噴射器、高壓管道,鋼結構和混凝土結構。池式反應器也是水平安裝,因此整個裝置的高度就會降低。
池式反應器中的特殊擋板防止回流,這樣利于達到化學平衡和反應更高的轉化率。這樣也使后面的高壓設備的尺寸縮小而使投資成本降低。
尿素裝置改造項目
目前由荷蘭斯塔米卡本公司提供對舊尿素裝置改造的幾種方案:
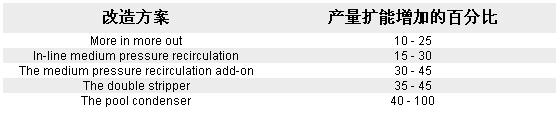
最終整個裝置能夠達到的產量和原大型設備設計余量有關。
More in more out方案 該方案主要內容為:
·在反應容器中安裝新的高效率板(提高反應的轉化率)
·合成部分需要充分利用原設計余量
·增加工藝和公用工程加熱器和冷凝器能力
In-line medium pressure recirculation 方案 該方案主要內容為:
·降低合成部分的回流水,同時提高3%~4%反應的轉化率
·安裝新的中壓回流部分(運轉壓力18bar),這部分是位于高壓二氧化碳汽提塔和低壓回流部分之間
The double stripper 方案 該方案主要內容為:
·合成部分并聯一個高壓二氧化碳的汽提塔,反應器輸出的尿素溶劑有一部分輸入至原二氧化碳的汽提塔,有一部分輸入至新安裝的汽提塔。
·增加蒸發和造粒設備是脫瓶頸的一部分
·此方案的極限是高壓氨基甲酸酯凝器的產量
池式冷凝器方案 該方案主要內容為:
·水平安裝高壓池式冷凝器可以提高冷凝能力和反應容積
·同double stripper方案一樣,需要并聯式安裝高壓二氧化碳汽提塔
·此方案適合于原不包含二氧化碳氣體尿素裝置的擴能,因為會明顯提高公用工程耗量
降低尿素裝置排放方案 該方案主要會降低尿素裝置的氨氣和二氧化碳排放量,同時會降低主要原料(氨氣和二氧化碳)的消耗量。改裝置內容主要為合成部分后面的低壓吸收裝置和回流部分的常壓吸收裝置改裝。所有的氨氣和二氧化碳的排氣(特別是尿素槽、氨水槽、低壓氨基甲酸酯冷凝器、回流冷凝器等)回流將會在吸收系統進行處理。
安裝高效吸收系統能獲得與接近理論值相近較低的消耗,同時也可以達到最高的排放標準,合成部分低壓吸收塔出口氨氣排放量低于0.5公斤/小時,,低壓回流部分常壓吸收塔出口氨氣排放量為0.5公斤/小時。